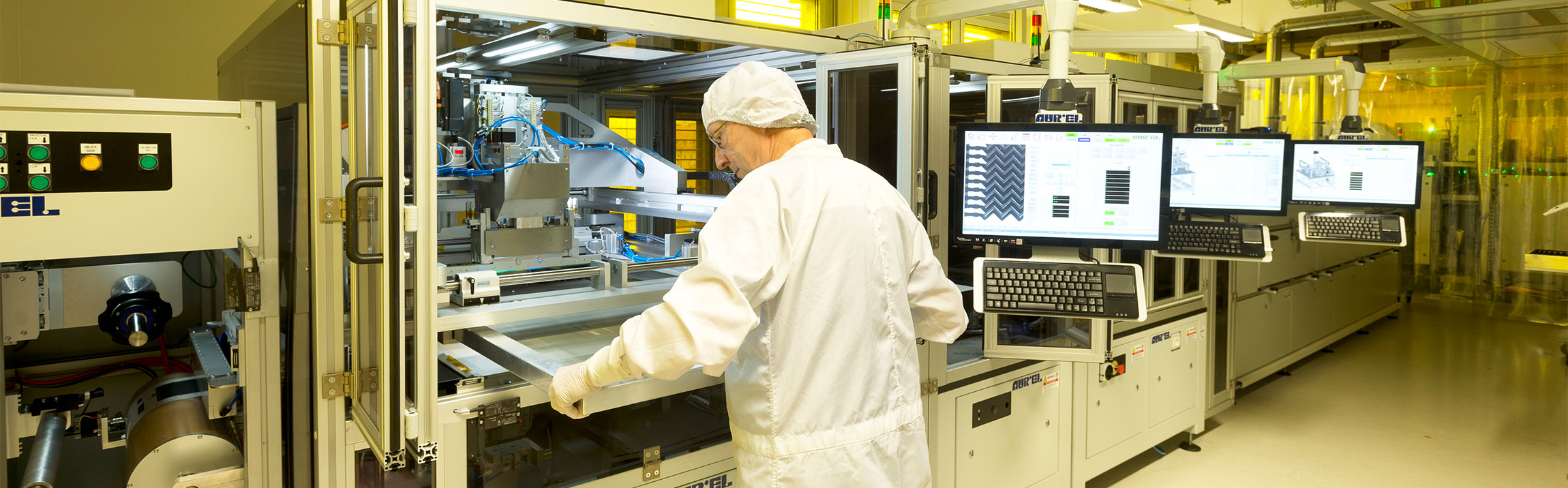
Screen printer in the Fraunhofer EMFT roll-to-roll pilotline for flexible hybrid electronics
“Flexible electronics” means manufacture of electronic components and systems on mechanically bendable substrates. „Flexible hybrid electronics” refers to the variety of manufacturing technologies that fit best for the targeted application. In addition to the well established technologies for the manufacture of wiring systems on flexible substrates, such as additive printing and lithographically defined and etched copper patterns, EMFT’s reel to reel pilot line for flexible hybrid electronics also comprises assembly, IC integration and packaging.
Metallization | Metallization of foil substrates with adhesive and conductive layers, e.g. with copper or chrome, using a sputtering system. The coating is carried out roll-to-roll with maximum substrate width of 215 mm. The equipment from the comany FHR additionally includes an IR heater for better outgassing of the layers, as well as inverse sputter etcher for surface activation. |
Lamination | Lamination of various foils under pressure and temperature using heated rolls. Typical applications are lamination of dry film resist for preparation of photolithopgraphic structuring, or passivation with adhesive-coated covering foils. The adjustable process parameters include: temperature, pressure and feed rate. The processing takes place in equipment from the company Stork. |
UV-Lithography | UV lithography for creating a mask structure in the resist of a layered foil system as a stop & go procedure. In addition to proximity and contact exposure the equipment includes an automatic pattern recognition for mask alignment. The equipment from the company Ciposa allows for processing or foil rolls of 215 mm in width with 9" masks. |
Development | For fixation and development of exposed resist layers a spray developer is used. At places where no resist remains after the development, the metallization can be galvanically strengthened or etched. The processing takes place with equipment from the company Höllmüller. |
Electroplating
|
Stripping of copper several µm thick on pre-metallized and structured polymer films (pattern plating), in a continuously operating galvanic equipment. The process is divided into pre-galvanic with low current and main galvanic with higher current. |
Etching | Even etching of mezallized foils in continuously operating spray-etch equipment. The modular construction enables fast change of etching medium, in order to be able to etch various metals. The processing takes place in equipment of the company Schmid. |
Plasma etching | Surface conditioning and etching of foils and polymers. Coatings in roll-to-roll throughfeed process using plasma equipment. Nitrogen, oxygen and CF4 are used as etching gases. |
Screen printing | Printing of various pastes (conductive paste, electroluminescence, dielectric, semiconductors) structured on a foil in a roll-to-roll screen printing equipment. In addition to subsequent drying with UV and convection, the equipment includes automatic pattern recognition capabilities for multilayer systems. |
Laser processing | Processing of foils with a UV laser (355 nm). Local stripping of material from the covering layer as trenches or holes. Cutting ghrough all foil layers is also possible. This enables opening vias, separating components from the composite foil, structuring layers, writing text or symbols for markings, or trimming film resistors. Alignment precision 50 µm. Processing is carried out with equipment from the company LS Systems. |
Rewinder | Winding of foil strips from one roll to the other, enabling exact merging and orthomorphic (true angles) cutting, parallel or perpendicular to the running direction of the foil. Left/right operation, web edge control, length measurement and adjustable strip tension enable optimal conditioning of the foil reels The processing takes place with equipment from the company db-matic. |
Pick & Laminate | Automatic assembly and electrical contacting of foil components (such as flexible batteries, displays, solar cells or other subsystems) on the base substrate, either on sheets or rolls. |
Digital UV-Photolithography | Maskless digital photolithographic roll-to-roll processes with lateral resolution upto 5 µm. The modern infrastructure enables continuous "step & repeat" processing of foils with extremely high registration accuracy and substrate width upto 305 mm with no length limitation. |
Roll-to-roll chip bonder | Reel-to-reel assembly of various components on foils, ranging from bare dies to SMD components from wafers, trays and rolls. Face-up or flip-chip assembly. Contacting techniques include soldering, ACA-assembly and conducting adhesives. |
3D stacking of foil electronics | A new system for stacking functional, large-area foil sheets on each other is under construction. This will open a new perspective to fabricate 3D-stacked chip-foil interposers at Fraunhofer EMFT. |